Aumenta la vida útil de tu equipo con estos tips.
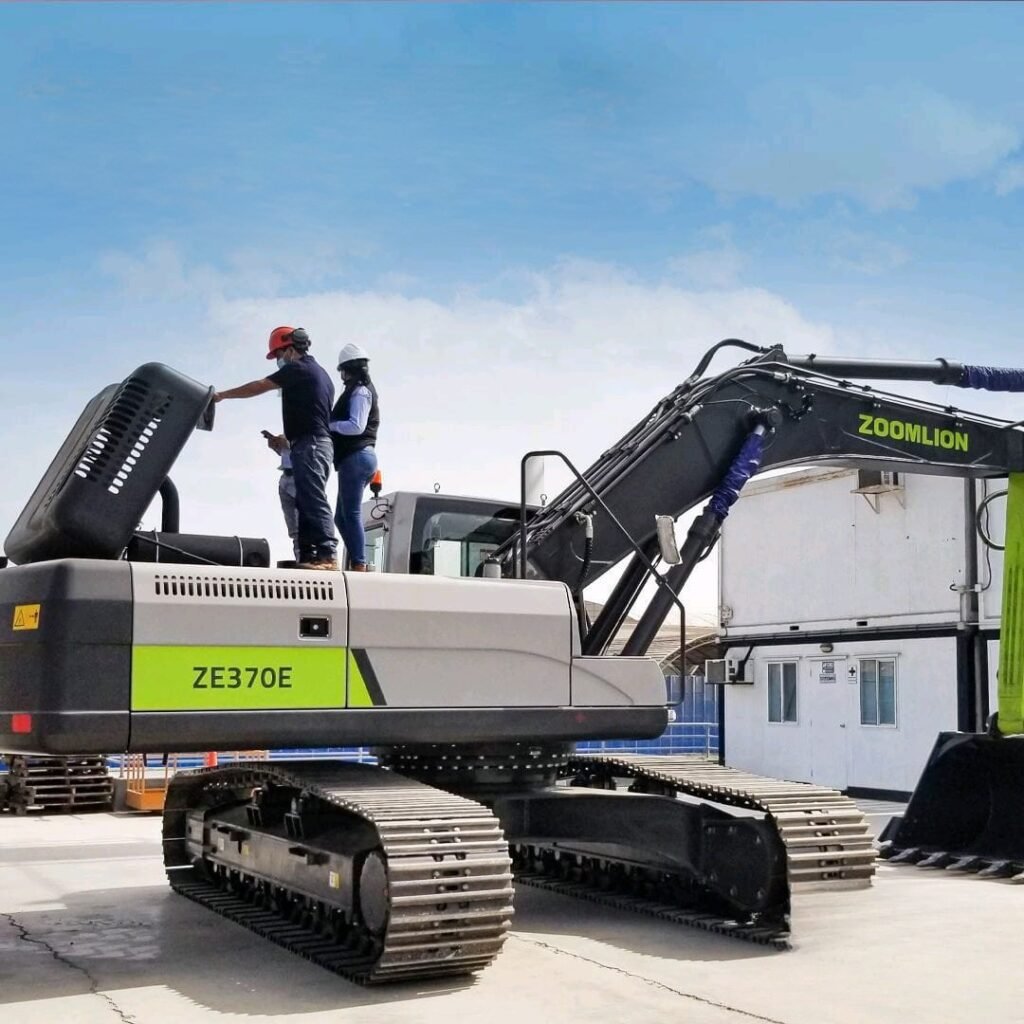
El mantenimiento preventivo en maquinaria pesada no es solo una práctica recomendada, sino una necesidad para garantizar la seguridad, productividad y rentabilidad de cualquier operación industrial. La falta de una estrategia de mantenimiento adecuada puede llevar a fallas inesperadas, paros operativos costosos y una reducción significativa en la vida útil del equipo. En esta guía técnica, te explicamos por qué es vital el mantenimiento preventivo, qué incluye y cómo implementarlo de manera eficiente.
El mantenimiento preventivo consiste en realizar inspecciones periódicas y acciones programadas con el fin de evitar fallas antes de que ocurran. A diferencia del mantenimiento correctivo, que solo actúa una vez que el problema ya está presente, el preventivo se enfoca en la anticipación. Este enfoque permite detectar desgastes, piezas sueltas, fugas, y cualquier signo de deterioro antes de que cause un daño mayor o una parada forzosa del equipo.
Los beneficios de un buen programa de mantenimiento preventivo son numerosos. En primer lugar, se prolonga la vida útil del equipo, permitiendo que funcione en condiciones óptimas durante más tiempo. También se reducen los costos de reparación, ya que atender una pieza desgastada es mucho más económico que reparar una avería total. Además, se mejora la seguridad en el sitio de trabajo, al disminuir las posibilidades de fallas durante la operación. Y, por supuesto, se aumenta la productividad al reducir tiempos muertos y evitar interrupciones imprevistas.
Para implementar un plan de mantenimiento preventivo efectivo, es fundamental contar con una bitácora de uso y un calendario de revisiones basado en el tipo de maquinaria, las horas de trabajo y las condiciones del entorno. Aquí algunos aspectos clave que debe incluir:
- Inspección visual diaria: Revisar el estado general del equipo antes y después de cada jornada. Buscar fugas, partes sueltas, cables dañados o ruidos inusuales.
- Cambio de lubricantes y filtros: Seguir las recomendaciones del fabricante y no esperar a que los componentes estén al límite de su funcionamiento.
- Revisión de sistemas hidráulicos y eléctricos: Verificar presión, niveles de fluidos, sensores, y posibles cortocircuitos o fallas eléctricas.
- Alineación y tensión de correas y cadenas: Mantener los sistemas de transmisión funcionando con precisión evita daños mayores.
- Revisión de neumáticos u orugas: El estado de los componentes de tracción influye directamente en el rendimiento, el consumo y la estabilidad del equipo.
- Capacitación del operador: Un operador capacitado no solo maneja mejor la maquinaria, también puede detectar anomalías a tiempo y reportarlas adecuadamente.
- Registro y seguimiento de incidencias: Toda intervención, por mínima que sea, debe ser registrada. Esto permite identificar patrones y mejorar las decisiones de mantenimiento a futuro.
Una recomendación clave es utilizar software de gestión de mantenimiento (CMMS, por sus siglas en inglés), que permite llevar un control automatizado de las tareas, programar revisiones, recibir alertas y generar reportes. Esto es especialmente útil cuando se cuenta con una flota grande o con equipos que operan en distintos turnos o ubicaciones.
Conclusión:
El mantenimiento preventivo en maquinaria pesada no solo alarga la vida útil del equipo, también mejora la seguridad y reduce costos operativos a largo plazo. Implementar un plan bien estructurado, basado en revisiones periódicas, monitoreo continuo y capacitación, es una de las decisiones más inteligentes que puede tomar una empresa. No se trata solo de reparar menos, sino de anticiparse, proteger la inversión y asegurar la continuidad operativa sin contratiempos. Un equipo bien mantenido es sinónimo de confianza y eficiencia en cualquier proyecto.